「本当に必要か分からないチェック業務」に追われ、日々の搾乳や牛の観察がおろそかに… そんな悩みを抱える酪農家は多いはずです。本記事では、ミス防止のために無闇に増えたルールと属人化の負のループを断ち切り、Lean〈リーン〉の視点から現場をスリム化・最適化する具体的手法を徹底解説します。
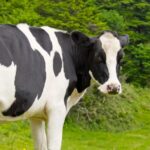
ルールは“増やす”より“磨く”が大事! 牛を見る時間を取り戻そう🐄
1. 問題提起:チェック地獄と属人化の負のスパイラル
多くの酪農現場で見られる流れ:
- 【ヒヤリハット報告義務化】→「提案しなきゃ」と形式チェック項目が爆増
- 仕組みを増やすほど運用が複雑化し、逆にヒヤリハットやミスが増加
- 属人化した業務はブラックボックス化し、新人もマニュアルも混乱状態に
この悪循環は、「1件の重大事故の背後に29件の軽微な事故、300件のヒヤリハット」という“ハインリッヒの法則”と同様の構造です。👉関連記事:酪農現場におけるハインリッヒの法則
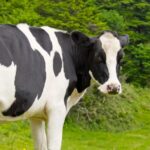
1つのミスの裏に300件のヒヤリが潜む。だからこそ“現場に合った対策”が必要
属人化のループ構造
- 属人化:特定の担当者しか手順を知らない
- ミス発生:責任追及→人的エラーをあぶり出す
- 仕組み追加:チェックリストや承認フローを増設
- 複雑化:運用負荷↑→新たなミス・属人化再発
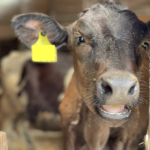
「この手順、◯◯さんしか分からない…」→ それ、属人化のはじまりです。
2. 効率化ジレンマ—給料構造と心理的抵抗
日本の多くの酪農場は「労働時間=給与」のモデル。効率化すると作業時間が減り、結果的に給料が下がると捉えられてしまいます。さらに:
- ベテランほど「慣れ」が強み。新システムで経験値が活かせない不安
- 「仕事が早く終わって暇そう」に見られるプレッシャー
- 上司になると「リスクを減らしたい」心理から変更をためらう傾向
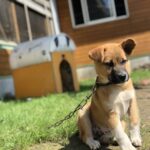
時給で働いてるのに効率化って…正直、給料どうなるの?
3. 解決策:Leanで“必要最小限”にリセット
3-1. 現状を「見える化」する
- バリューストリームマップ(VSM)で作業フローを図式化し、手戻りや待ち時間を可視化
- ABC分析で作業を分類
- A:高頻度・高価値 → 継続強化
- B:低頻度・高価値 → 定期的に見直し
- C:低頻度・低価値 → 即削減 or 自動化検討
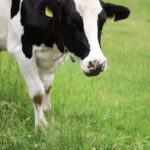
“なんとなくやってる作業”、ぜんぶ見える化して棚卸ししよう!
3-2. 「ムダな仕組み」を削る
- ヒヤリハットは再発防止策にフォーカス:一時チェックより教育・設備改善を優先
- 日常チェックリストは日次→週次/月次に集約して負担を軽減
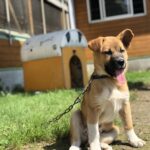
“再発防止”って、チェックを増やすことじゃなかったんだ…!
3-3. 属人化を防ぐ「多能工化」とデジタル化
- ジョブローテーションで複数業務を経験させ、知識を共有
- ポカヨケ(ミス防止治具)導入:色分けバンドや固定治具で誰でも正確作業
- QRコードマニュアル+写真・動画で手順をデジタル化し、最新版をリアルタイム共有
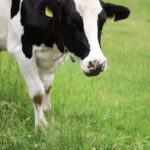
赤は抗生剤で出荷停止、黄色は盲乳って決めたら迷わない!
4. 小規模酪農で使えるベストプラクティス
テーマ | 実例 | 効果 |
---|---|---|
現場ウォーク | 朝の搾乳前に10分間「現場巡回」 | リスク・発情の早期発見+詳細チェックの削減 |
PDFマニュアル配布 | 重要手順のみPDF化しタブレットで共有 | 印刷コスト削減+常に最新版閲覧可能 |
動画マニュアル | QRコードから動画手順にアクセス | 新人育成時間を30%削減 |
月次ワークショップ | 「属人化・複雑化リスト」を全員でレビュー | 改善アイデア15%増加+実行率アップ |
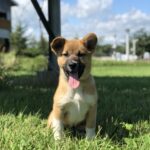
結局、生き物相手の仕事だから臨機応変に対応しなきゃ!
固定のマニュアルだけでは対応できないこともある。知識をつけよう!
5. よくある質問(Q&A)
Q. チェックリストを全部やめても大丈夫? A. 全部削除ではなく、重要度でランク付け。Aランクのみ日常、B/Cランクは週次・月次で。
Q. ベテランの抵抗をどう乗り越える? A. 「経験値データ」を可視化し、現状と改善後の数値差を示すことで納得感を醸成。
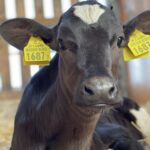
データに出して可視化することで見えてくるものも!
6. まとめ&次のステップ
- VSM・ABC分析で真のムダを見極める
- チェック項目を重要度で取捨選択し、日次/週次へ集約
- 多能工化+ポカヨケ・QRマニュアルで属人化解消
- PDCAで仕組みを「使われる価値あるもの」に育てる
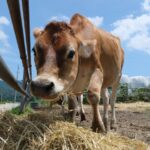
次の一歩は「現場のムダ1つ」を見つけて、対話から始めること。
本記事が「無駄なチェック業務」と「属人化」という2大課題の解消に役立てば幸いです。 ▼関連記事 – 酪農業界の評価制度と人材育成のポイント
– 酪農現場におけるハインリッヒの法則とは?
コメント